 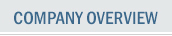 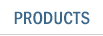 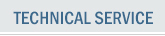 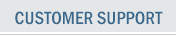 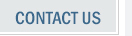 |
|
 |
 |
Characteristics
| Plenco's Commitment | Typical
Applications for Phenolic Molding Materials
Plastics Engineering Company manufactures a full
range of phenolic molding materials. Plenco thermoset
compounds are suitable for evaluation in industrial
and consumer applications, which require molded
properties to be maximized, but unit cost to be
minimized. Plenco phenolic two-stage, single-stage,
and pigmented molding materials are produced in
granular, nodular, and briquette forms.
Plenco thermoset phenolic molding material is manufactured
with state-of-the-art process control and quality
management systems to ensure the highest product
quality and uniformity. At a relatively low unit
cost, Plenco phenolic molding materials offer outstanding
long-term engineering performance when exposed,
under load, to elevated temperature. Additionally
phenolic materials have excellent chemical resistance,
electrical insulation, surface hardness, and dimensional
stability.
In the design of Plenco phenolic molding materials,
specific base-resin properties, filler composition,
lubricants, and moisture content are important to
a particular application. Key formulation properties,
such as plasticity, extent of flow, and particle
size help to ensure cost-effective and highly productive
molding. All of this offers Plenco customers an
optimized combination of characteristics, which
are available for knowledgeable material selection.
Formulations are typically engineered with two-stage
phenolic resins for a broad range of molded properties
and processing latitude. Single-stage phenolic resins
contribute to long-term service in those applications
requiring moisture and steam exposure, and minimum
corrosion. When the end product calls for bright
and stable computer-matched color, Plenco offers
a unique line of melamine-phenolic copolymer molding
materials.
top
Characteristics
Thermal Performance
It is often recognized in the evaluation of available
plastics for a given application that the outstanding
characteristic of cured thermoset phenolic molding
material is excellent thermal performance. This
is especially significant when consideration is
given to the relatively low unit cost of these materials.
Thermal performance refers to the ability of a molded
plastic product to maintain its structural integrity,
under mechanical load during a prolonged exposure
to elevated temperatures. The thermal performance
of polymer systems is closely related to their glass
transition temperature (Tg). This is the temperature
at which the molecules rapidly gain in their mobility
as the cured molded sample is heated. Even in the
presence of fillers and reinforcements that provide
the apparent initial rigidity, exposure to temperatures
above the Tg will usually cause a polymer to flow
or creep under load.
Engineered Creep Resistance
The relatively high glass transition temperature
of cross-linked polymers, such as phenolic, results
in excellent resistance to creep under mechanical
load. A unique property of cured phenolic is the
ability to raise its Tg by a carefully controlled
post bake protocol, after the part is molded. When
correctly applied, the post bake program can result
in a further improvement in creep resistance, dimensional
stability, and modulus (stiffness) at elevated temperature.
Dynamic Mechanical Properties
Dynamic mechanical analysis (DMA) is a powerful
analytical tool for characterizing the thermal properties
of polymers. The important feature of DMA is that
the physical measurements of storage and loss modulus
are made so gently that the sample is not damaged.
It is therefore possible to observe the changes
in modulus as a third parameter, such as temperature,
is varied. With this and other analytical techniques,
Plenco chemists and engineers, who have achieved
a considerable understanding of the post bake process,
are available to assist in the optimization of dynamic
mechanical properties and thermal performance of
your cured phenolic parts. Reports on post baking
and its effect on the glass transition temperature
that are published by Plenco are available upon
request.
Heat Resistance
Because of excellent thermal performance, phenolic
molding materials are specified to insulate and
protect sensitive components from the adverse effect
of high temperature exposure. Plenco manufactures
a wide range of phenolic molding materials designed
for high temperature use. These grades are formulated
with resole or novolac resin systems, and specially
selected fillers and reinforcements, in order to
meet end use specifications. Consumer safety is
enhanced when the potential for the end product
to overheat, melt or initiate a fire is minimized
through the selective use of a heat resistant phenolic
molding material. Plenco heat resistant phenolic
grades are the materials of choice for automotive
under-the-hood parts, cookware handles and knobs,
and electrical appliance components.
Underwriters Laboratories Ratings
Phenolic molding materials are listed by Underwriters
Laboratories with a generic Relative Thermal Index
of 150� C. this listing is based on the excellent
75-year safety record of molded thermoset phenolic
components used in electrical and consumer products.
Especially noteworthy is Plenco 06582, a modified
phenolic formulation, which is UL yellow card listed
at 180� C.
Careful formulation of Plenco phenolic molding materials
makes them ideal candidates in applications requiring
optimum flammability characteristics. Unlike many
thermoplastic resins, phenolic molded parts, when
exposed to an ignition source, do not drip flaming
particles, a potential ignition source. Plenco phenolic
molding materials are tested and classified according
to the UL 94 Flammability Standard as HB, V-1, or
V-0. Typical applications specifying these ratings
include appliance components, electrical distribution
products, and housewares applications.
Dimensional Stability
Many of Plenco's phenolic molding materials are
formulated to provide tight dimensions with minimal
deformation under mechanical load at elevated temperatures.
This characteristic is critical when considering
calibration requirements, screw-torque retention,
and dimensional specifications to prevent thermal,
mechanical, or electrical failure, especially during
thermal cycling of end used products. For this reason,
power train components, electrical motor housings,
brush cards, control housings, and telecommunication
connectors specify phenolic formulations.
Self-Lubrication
Plastics Engineering Company offers several unique
phenolic molding materials enhanced with graphite,
PTFE, and other internal lubricants. These formulations
provide excellent lubricity and abrasion resistance
for components that require repeated mechanical
cycling or part-to-part contact. A key advantage
of components molded from these materials is their
ability to maintain surface smoothness after mechanical
lapping. Plenco self-lubricating phenolic materials
are used in gas metering devices, fuel impellers,
toggle switches, seals, and bearings.
Plenco's
Commitment
Plenco's accredited Resin Research and Materials
Engineering Laboratories, extensive resin manufacturing
and compounding facilities, and ongoing technical
sales efforts are direct indications of a strong
dedication to building strategic relationships with
our customers. Plenco has the capacity to deliver
large quantities of consistent and high quality
thermoset molding materials that meet or exceed
customer specifications. Additionally, we have a
philosophy of continual product improvement and
cost containment. All of this is supported with
in-depth engineering suggestions for tooling and
part design, and assistances with prototype molding.
And finally, there is Plenco's responsive distribution
center offering custom handling and efficient, on-time
delivery, often in Plenco's own fleet of trucks.
The combined effort of materials engineering and
manufacturing at Plenco, along with good communication
with our customers, is key in developing value-added
end-product characteristics. While many of Plenco's
formulations are suitable for evaluation in typical
applications, often our molding materials are the
result of customized development and engineering
to match specific molding situations or end-use
requirements of individual customers. This results
in a wide range of phenolic formulations and plasticity
grades. We look forward to working with you to explore
the application of Plenco phenolic molding materials
in your process or product application. Detailed
data reports and price schedules are available upon
request.
After the engineering and development program is
completed and the tooling is in place, Plenco will
provide an experienced group of technical service
personnel, who offer out customers assistance in
processing initial samples for their fitness-for-use
testing, or in solving problems in production processing.
We will do our best to help out immediately by phone
or fax, or if you wish we will come to your plant
promptly. Our strong commitment to polymer science
research, together with the design of innovative
molding materials, proves Plenco to be a leader
in the thermoset phenolic industry.
Typical Applications
for Phenolic Molding Materials
- Cookware handles and knobs
- Electrical terminal strips
- Drive train components, brake components,
engine oil fill caps, and motor and alternator
components
- Small appliance parts, such as steam iron
skirts, range strips, appliance plug parts,
houseware items, and popcorn popper chutes
- Gas meter parts
- Bottle and container covers and closures
- Electrical applications, such as switch housings,
circuit breaker cases, fuse holders,
lighting baffles, snap-switch housings, capacitor
caps, connectors, and commutators
- Parts for automotive interiors
top
|
|
|
|
|
|
|